Difference between revisions of "Transition to Turbulence"
(→Complex flow) |
|||
(171 intermediate revisions by 2 users not shown) | |||
Line 1: | Line 1: | ||
− | ''Created by [[User:Ian|Ian Nesbitt]] and [[User:Julialiu18|Jukes Liu]] on 2019-02-19'' | + | ''Created by [[User:Ian|Ian Nesbitt]] and [[User:Julialiu18|Jukes Liu]] on 2019-02-19. Because this page has some high-resolution animations, it is best viewed on a reliable internet connection.'' |
+ | __NOTOC__ | ||
− | + | Welcome to our teaching module exploring the '''transition to turbulence''' through models of fluid flow around a cylinder! | |
+ | |||
+ | Transitioning to turbulence involves decreasing the predictability of a system. Inertial forces begin to dominate over viscous forces, resulting in more chaotic particle motion in the system ''(take a quick look at the Hurricane Irene example below in the Complex Flow section)''. In this module, we will explore this transition and learn how viscosity affects the dynamics of a fluid flowing around a cylindrical impediment. We can observe an interesting phenomenon called Von Kármán Vortex Streets at this simulated transition to turbulence. These naturally-occurring phenomena are fascinating and have many natural and engineering implications. By the end of the module, you should be able to describe what's occurring in each of the scenarios presented and have a good grasp on the dynamics involved in the complex flow examples. You will be able to describe the initial conditions of a system, the transition from laminar to turbulent flow, and the effect viscosity has on the inertia, complexity, and predictability of a system! | ||
+ | |||
+ | Below is a snapshot of one of our computational models of water flowing past a cylinder. In this early time-step, we can see an instability begin to develop in the wake of the cylinder. | ||
+ | |||
+ | |||
+ | [[File:Water Vort VelMagVectors.0134.png|none|800px|Early-timestep vorticity map of a numerical model of water flowing past a cylinder, showing an instability developing in the wake of the cylinder.]] | ||
+ | |||
+ | |||
+ | Here is a satellite loop of a von Karman Vortex Street developing in the wake of Guadalupe Island off the coast of Baja California, Mexico. (source: twitter user [https://twitter.com/weatherdak/status/1128453166725353473 @weatherdak]) | ||
+ | |||
+ | [[File:GuadalupeVonKarman.mp4|none|1000px]] | ||
= Overview = | = Overview = | ||
− | In | + | In order to model the transition to turbulence and the effects of changing viscosity on the dynamics of a simple fluid system with a single cylindrical impediment placed in the flow path, we use several modeling tools: [https://www.comsol.com/ COMSOL Multiphysics], [https://en.wikipedia.org/wiki/Smoothed-particle_hydrodynamics Smoothed-Particle Hydrodynamics] (SPH), and [https://www.paraview.org/ ParaView]. We will describe the model set-up and its physical basis, the differences between the three scenarios with fluids of different viscosities, and several real-world implications. We will move from looking at the behavior of more viscous fluids and move towards fluids with lower viscosities. Note: [https://en.wikipedia.org/wiki/Viscosity Viscosity] is defined as the measure of a fluid's resistance to deformation. |
− | |||
− | We will move from looking at | ||
First, let's start by learning how to talk about the various components of flow. | First, let's start by learning how to talk about the various components of flow. | ||
Line 15: | Line 26: | ||
When we talk about fluid flow, we need to first describe the fluid. Some of the fundamental characteristics of fluid are density, viscosity, compressibility, heat capacity, and thermal conductivity. In this exercise we will ignore the thermal properties entirely, define a constant density and compressibility, and focus most of our attention on how viscosity affects the kinematics of a fluid system. | When we talk about fluid flow, we need to first describe the fluid. Some of the fundamental characteristics of fluid are density, viscosity, compressibility, heat capacity, and thermal conductivity. In this exercise we will ignore the thermal properties entirely, define a constant density and compressibility, and focus most of our attention on how viscosity affects the kinematics of a fluid system. | ||
− | Compressibility and density are fairly easy to define. [https://en.wikipedia.org/wiki/Compressibility Compressibility] is the tendency of a fluid to change its volume due to changes in pressure. Since we are not dealing with immense pressure, we assume that compressibility is zero across all models. [https://en.wikipedia.org/wiki/Density Density] is the quantity of mass per unit volume. For the purposes of this model, we will hold density constant at 1 kg m<sup>-3</sup> to try and isolate the effects of viscosity. | + | Compressibility and density are fairly easy to define. [https://en.wikipedia.org/wiki/Compressibility Compressibility] is the tendency of a fluid to change its volume due to changes in pressure. Since we are not dealing with immense pressure, we assume that compressibility is zero across all models. [https://en.wikipedia.org/wiki/Density Density] is the quantity of mass per unit volume. For the purposes of this model, we will hold density constant at 1 kg m<sup>-3</sup> (approximately that of freshwater) to try and isolate the effects of viscosity. These parameters will be fed into the Navier-Stokes fluid momentum equation (below) for each location in the model at each time step. |
− | + | === Navier-Stokes momentum equation === | |
− | |||
− | |||
− | |||
− | |||
− | |||
− | |||
− | + | To characterize the motion of particles in the fluid, we must account for the changes in momentum. This Navier-Stokes equation is derived based on the conservation of momentum in a system. It is the foundation of our models. This equation can be broken down into its different terms, which represent the effects of the inertial forces, body forces, viscous forces, and the pressure gradient throughout the system. | |
− | |||
− | |||
− | |||
− | |||
− | |||
− | |||
− | |||
− | |||
− | |||
− | |||
− | |||
− | + | This is the basic structure of the Navier-Stokes momentum equation: | |
− | + | Mass * acceleration = Body forces + Shear forces - Pressure gradient | |
− | + | These qualitative terms are represented by some greek symbols which may or may not mean anything to you right now, but we'll break them down for you. | |
− | |||
− | + | ρ (∂v / ∂t) = Δρg + µ∇<sup>2</sup>U - ∇P | |
{| class="wikitable" style="" | {| class="wikitable" style="" | ||
Line 66: | Line 59: | ||
|- | |- | ||
|'''∇<sup>2</sup>U''' | |'''∇<sup>2</sup>U''' | ||
− | |= | + | |= curvature of velocity field (2nd derivative) |
|- | |- | ||
|'''∇P''' | |'''∇P''' | ||
Line 72: | Line 65: | ||
|} | |} | ||
− | The inertial forces (acceleration) is represented by ∂v / ∂t. On the right hand side of the equation, we have the body forces (ρg), viscous forces ( µ∇<sup>2</sup>U), and the pressure gradient (∇P). | + | The inertial forces (acceleration) is represented by '''∂v / ∂t'''. |
+ | |||
+ | On the right hand side of the equation, we have the body forces from density and gravity ('''ρg'''), viscous forces from the viscosity property of the fluid ('''µ∇<sup>2</sup>U'''), and the pressure gradient throughout the system ('''∇P'''). Each of these forces will influence the acceleration or motion of particles. Can you visualize how these different forces on the right-hand side of the equation might influence a particle's motion? | ||
+ | |||
+ | Solving this equation for each grid point or particle at each time step will define how our fluid will behave in a computational sense. Once our fluid starts to move, we need ways to describe how it is flowing. Fluid flow can be characterized as either laminar or turbulent, which has to do with the predictability of its motion throughout the system. The parameter that is used to describe this characteristic is called the Reynolds number. | ||
+ | |||
+ | === Reynolds number and things that affect it === | ||
+ | |||
+ | The Reynolds number, ''Re'', is a dimensionless number that represents the flow regime of a fluid. The Reynolds number is a way of representing whether a flow is laminar, transitional, or fully turbulent using numerical values. When flow is laminar, the fluid motion is more uni-directional, smooth, and more predictable. Imagine the flow of molasses being poured out onto a table. Another example would be toothpaste being squeezed out of the tube. Laminar flow is represented by lower Reynolds numbers. When flow is turbulent, fluid motion is more irregular. A gust of wind flowing around a flag-pole causing the flag to flap behind it is an every-day example of a more turbulent flow. These flows are characterized by higher Reynolds numbers. | ||
+ | |||
+ | What are some other real-world examples of fluid flow that you can think of? Would you characterize the flow as more laminar or turbulent? | ||
+ | |||
+ | ==== Viscosity ==== | ||
+ | |||
+ | [[File:Shearthinthick.png|thumb|400px|Viscous regimes. Newtonian fluids exhibit a linear relationship between stress and strain rate. This means that deformation occurs proportional to the forces acting on the fluid. (Image from https://neutrium.net/fluid_flow/viscosity/)]] | ||
+ | |||
+ | Keeping those real-world examples in mind, we can brainstorm about the differences in those fluid systems that might affect the flow pattern. There are differences in the fluid properties between the molasses, toothpaste, and atmospheric air. Once of the main differences, which we examine in depth in this module, is their difference in viscosity. "Viscosity" is a term you might be familiar with in terms of describing a fluid. The technical definition of [https://en.wikipedia.org/wiki/Viscosity viscosity] is a fluid's capability of resisting deformation. Molasses and toothpaste are more viscous than water, which means that their flow is more difficult to deform or disturb. Meanwhile, air has a much lower viscosity and is quite easily deformed! We deform air every time we move. Therefore, if everything else is held constant, increasing viscosity decreases the Reynolds number which means that fluid flow becomes more laminar. If we decrease viscosity, fluid flow will begin to transition towards turbulence. | ||
+ | |||
+ | The conceptual diagram at right shows viscous regimes. A fluid that exhibits a linear relationship between stress and strain is described as '''Newtonian'''. Any force that is applied to Newtonian fluids results in a proportional amount of deformation. '''Shear thickening''' is a term used to describe a nonlinear regime in which greater force can result in less deformation (corn starch and water, for example...watch a very British demonstration of this behavior [https://youtu.be/BN2D5y-AxIY?t=8 here]). Conversely, '''shear thinning''' describes a fluid that deforms more easily with increased force (think about paint - it runs readily when applied with a brush or roller, yet just moments after retains enough viscosity to stay in place with minimal running). | ||
+ | |||
+ | ==== Velocity ==== | ||
+ | |||
+ | Another main parameter that influences the flow regime is the velocity of the fluid. Faster-flowing fluids tend to result in more turbulent responses. In the air around a flagpole example, higher wind velocity will result in a more turbulent response which one would observe as more violent "flapping". | ||
+ | |||
+ | Therefore, Reynolds number is a function of viscosity and velocity: f(µ, v). Velocity and viscosity have inverse influences on the Reynolds number (i.e. as velocity increases, the Reynolds number increases while increasing viscosity lowers the Reynolds number). This module will walk you through the transitions that occur when we decrease '''viscosity''' while holding everything else, including velocity, constant. We are choosing to focus on examining the effects of lowering viscosity by examining fluid flow fluids with different viscosities (honey, water, air) while holding the velocity constant. This would have a similar effect as increasing velocity and holding viscosity constant. Using our models, we examine the effects of changing viscosity, effectively changing the Reynolds number, on fluid flow. | ||
+ | |||
+ | As we have introduced above, the Reynolds number is an extremely useful way to characterize flow conditions. The ''Re'' number is equal to the '''inertial forces''' (velocity times characteristic length) over the '''resisting forces''' (viscosity). | ||
+ | |||
+ | Re = ρVD/µ = VD/v | ||
+ | |||
+ | {| class="wikitable" style="" | ||
+ | !colspan=2|where | ||
+ | |- | ||
+ | |'''V''' | ||
+ | |= fluid velocity (m s<sup>-1</sup>) | ||
+ | |- | ||
+ | |'''D''' | ||
+ | |= linear dimension (m) | ||
+ | |- | ||
+ | |'''µ''' | ||
+ | |= dynamic viscosity (Pa s) | ||
+ | |- | ||
+ | |'''v''' | ||
+ | |= kinematic viscosity (Pa s) | ||
+ | |- | ||
+ | |'''ρ''' | ||
+ | |= density (kg/m<sup>3</sup>) | ||
+ | |} | ||
+ | |||
+ | |||
+ | Note: ''Re'' can also be thought of as inversely related to how well flow conditions can be described mathematically across a given dimension (''x'', ''y'', ''z'', or ''time''). | ||
+ | |||
+ | |||
+ | The table below lists the qualitative descriptions for each quantitative ''Re'' range. | ||
+ | |||
+ | {| class="wikitable" style="text-align:center" | ||
+ | !colspan=3|Quantifying qualitative descriptions of Reynolds number | ||
+ | |- | ||
+ | |Laminar | ||
+ | |Transitional | ||
+ | |Turbulent | ||
+ | |- | ||
+ | |''Re'' < 100 | ||
+ | |100 < ''Re'' < 10<sup>5</sup> | ||
+ | |10<sup>5</sup>< ''Re'' | ||
+ | |} | ||
+ | |||
+ | Flows with Reynolds numbers of less than 100 are considered "laminar," while those from 100 to 10<sup>5</sup> are "transitional," and above 10<sup>5</sup> are "turbulent." At low Reynolds numbers (Re < 100), viscous forces dominate and flow is laminar. As the Reynolds number increases, due to lower velocity or higher viscosity, inertial forces begin to play a greater role and flow becomes increasingly turbulent. In this transition between laminar and turbulent flow, we begin to observe some unique fluid phenomena. Let's first describe our model and then take a look at these phenomena! | ||
− | = | + | = Model setup = |
=== Geometry === | === Geometry === | ||
− | Below is the geometry of our simple model | + | Below is the geometry of our simple model for fluid flow described by Navier Stokes equation (above) and solved as a finite-element model with help from numerical methods of COMSOL. |
+ | |||
+ | [[File:Geometry of cylinder model.png|none|COMSOL model geometry]] | ||
+ | |||
+ | This is a two-dimensional COMSOL model, which assumes that the horizontal (long) walls and the walls of the cylinder have a "no slip" condition. This means that as the flow gets closer to the wall, velocity goes to zero. This condition sets up a velocity gradient (shear) between the walls at zero and the center of the flow. The wall on the far left side has an inflow condition of 1 meter per second, and the wall on the right side has a zero-pressure outlet condition, which lets flow pass out of the model unhindered. | ||
− | + | COMSOL solves a finite element model, which means that it performs calculations for a mesh grid at each step. We use a relatively small mesh cell size ("Extra Fine" setting in COMSOL) on the order of ~1 cm. | |
− | + | [[File: meshdetail.png|600px|COMSOL model mesh]] | |
When we run the model, we are executing a variation of the Navier-Stokes momentum equation for each mesh element of the model at each time step. This equation, shown above, is fundamental to describing the behavior of fluids in continuum mechanics. | When we run the model, we are executing a variation of the Navier-Stokes momentum equation for each mesh element of the model at each time step. This equation, shown above, is fundamental to describing the behavior of fluids in continuum mechanics. | ||
− | === | + | === Experimental variable: Viscosity === |
− | Let's look at the viscosities of fluids we'll be working with. | + | Let's look at the dynamic viscosities of fluids we'll be working with. |
{| class="wikitable" style="text-align:center" | {| class="wikitable" style="text-align:center" | ||
Line 93: | Line 157: | ||
!µ (viscosity at 20 ºC) | !µ (viscosity at 20 ºC) | ||
|- | |- | ||
− | |'''Honey''' | + | |'''1. Honey''' |
|1 * 10<sup>1.5</sup> Pa s | |1 * 10<sup>1.5</sup> Pa s | ||
|- | |- | ||
− | |'''Water''' | + | |'''2. Water''' |
|0.89 * 10<sup>-3</sup> Pa s | |0.89 * 10<sup>-3</sup> Pa s | ||
|- | |- | ||
− | |'''Air''' | + | |'''3. Air''' |
|1.81 * 10<sup>-5</sup> Pa s | |1.81 * 10<sup>-5</sup> Pa s | ||
|} | |} | ||
− | + | As mentioned above, we use an initial fluid velocity of 1 m/s in all of our models. | |
+ | |||
+ | === Questions to consider === | ||
From the diagram of the model geometry, what is the linear dimension (D)? In this model, it is equivalent to the diameter of the cylinder. | From the diagram of the model geometry, what is the linear dimension (D)? In this model, it is equivalent to the diameter of the cylinder. | ||
Line 109: | Line 175: | ||
Before we go through the model results, try calculating the initial Reynolds numbers for each fluid viscosity using the linear dimension and the fluid velocity. Based on the Reynolds number calculated for the honey, do you think the fluid flow will be more laminar or turbulent? What about for water? Air? | Before we go through the model results, try calculating the initial Reynolds numbers for each fluid viscosity using the linear dimension and the fluid velocity. Based on the Reynolds number calculated for the honey, do you think the fluid flow will be more laminar or turbulent? What about for water? Air? | ||
− | == Honey (''μ'' = 10<sup>1.5</sup> Pa s) == | + | = Models = |
+ | |||
+ | == 1) Honey (''μ'' = 10<sup>1.5</sup> Pa s) == | ||
− | In the first example, we have a fluid with the viscosity of about that of honey, ''μ'' = 10<sup>1.5</sup> Pascal seconds (Pa s). You might imagine honey to be pretty " | + | In the first example, we have a fluid with the viscosity of about that of honey, ''μ'' = 10<sup>1.5</sup> Pascal seconds (Pa s). You might imagine honey to be a pretty "stiff" liquid, which has something to do with its viscosity. What do you think will happen? Let's look at a few parameters of flow in the honey model. |
− | === Velocity (x component) === | + | === Velocity 1 (x-component) === |
[[File:Mu101.5_ux1_velocity.gif]] | [[File:Mu101.5_ux1_velocity.gif]] | ||
Things are pretty orderly and logical here. Not a whole lot changes over time. You might describe this flow system as "'''[https://en.wikipedia.org/wiki/Laminar_flow laminar]'''," since you can describe what will happen at any given point in the model space at any given time fairly easily. Note that velocity is highest near the cylinder where the honey must "squeeze by" the cylinder in order to keep up with the 1 m s<sup>-1</sup> inflow rate. This sets up a steep velocity gradient near the no-slip boundary of the cylinder, which we can see in the shear rate: | Things are pretty orderly and logical here. Not a whole lot changes over time. You might describe this flow system as "'''[https://en.wikipedia.org/wiki/Laminar_flow laminar]'''," since you can describe what will happen at any given point in the model space at any given time fairly easily. Note that velocity is highest near the cylinder where the honey must "squeeze by" the cylinder in order to keep up with the 1 m s<sup>-1</sup> inflow rate. This sets up a steep velocity gradient near the no-slip boundary of the cylinder, which we can see in the shear rate: | ||
− | === Shear rate === | + | === Shear rate 1 === |
[[File:Mu101.5 ux1 shear.gif]] | [[File:Mu101.5 ux1 shear.gif]] | ||
[https://en.wikipedia.org/wiki/Shear_stress Shear rate] is by definition the derivative of the velocity field, so it is no surprise that the highest shear values are in the areas next to the cylinder where the steep velocity gradient exists. If we break shear down into its component parts, we get [https://en.wikipedia.org/wiki/Vorticity vorticity]. Vorticity is the curl of the velocity field, or in other words, the rate of rotation of the angle between two particles as they slip past each other. | [https://en.wikipedia.org/wiki/Shear_stress Shear rate] is by definition the derivative of the velocity field, so it is no surprise that the highest shear values are in the areas next to the cylinder where the steep velocity gradient exists. If we break shear down into its component parts, we get [https://en.wikipedia.org/wiki/Vorticity vorticity]. Vorticity is the curl of the velocity field, or in other words, the rate of rotation of the angle between two particles as they slip past each other. | ||
− | === Vorticity === | + | === Vorticity 1 === |
[[File:Mu101.5 ux1 vorticity.gif]] | [[File:Mu101.5 ux1 vorticity.gif]] | ||
Again, unsurprisingly, the curl is highest where the gradient of velocity is high. This makes sense because as two particles slip past each other at different velocities, their orientation changes (rotates) with regards to one another. Vorticity will be highest near the no-slip boundaries in a simple laminar system like this. | Again, unsurprisingly, the curl is highest where the gradient of velocity is high. This makes sense because as two particles slip past each other at different velocities, their orientation changes (rotates) with regards to one another. Vorticity will be highest near the no-slip boundaries in a simple laminar system like this. | ||
− | === Pressure === | + | === Pressure 1 === |
[[File:Mu101.5 ux1 pressure.gif]] | [[File:Mu101.5 ux1 pressure.gif]] | ||
The pressure field should also make sense, because our one obstacle in this model sets up the overall gradient from inflow to outflow pretty nicely. Notice that the pressure values are very slightly higher on the [https://en.wiktionary.org/wiki/stoss stoss side] and slightly lower on the [https://en.wiktionary.org/wiki/lee lee side] of the cylinder. Note also that pressure gradients define the shortening and stretching of a system. Flow is shortened as it is forced towards the front of the cylinder and stretched as it goes past the cylinder. | The pressure field should also make sense, because our one obstacle in this model sets up the overall gradient from inflow to outflow pretty nicely. Notice that the pressure values are very slightly higher on the [https://en.wiktionary.org/wiki/stoss stoss side] and slightly lower on the [https://en.wiktionary.org/wiki/lee lee side] of the cylinder. Note also that pressure gradients define the shortening and stretching of a system. Flow is shortened as it is forced towards the front of the cylinder and stretched as it goes past the cylinder. | ||
− | === Reynolds number === | + | === Reynolds number 1 === |
[[File:Mu101.5 ux1 reynolds.gif]] | [[File:Mu101.5 ux1 reynolds.gif]] | ||
[https://en.wikipedia.org/wiki/Reynolds_number Reynolds number] describes how chaotic a system is. Since our system has almost no chaos, this plot is pretty boring at this viscosity. | [https://en.wikipedia.org/wiki/Reynolds_number Reynolds number] describes how chaotic a system is. Since our system has almost no chaos, this plot is pretty boring at this viscosity. | ||
+ | You may have noticed that the Reynolds numbers shown here are different orders of magnitude than those you calculated earlier. That's because the Reynolds numbers calculated via COMSOL are cell Reynolds numbers. This means that the Reynolds number is calculated using the characteristic length scale of the mesh grid size rather than the whole system. Despite this distinction, examining relative Reynolds numbers throughout the model will be useful for qualitatively describing what's happening with the flow. | ||
− | === Discussion === | + | === Discussion 1 - Honey === |
[[File:Honey-miel.jpg|thumb|"The high viscosity of honey results in perfectly laminar flow when poured from a bucket, while the low surface tension allows it to remain sheet-like even after reaching the fluid below. ... when the flow meets resistance it slows and [shortens by folding] upon itself."[https://en.wikipedia.org/wiki/Reynolds_number#Object_in_a_fluid] (used under Creative Commons 2.0)]] | [[File:Honey-miel.jpg|thumb|"The high viscosity of honey results in perfectly laminar flow when poured from a bucket, while the low surface tension allows it to remain sheet-like even after reaching the fluid below. ... when the flow meets resistance it slows and [shortens by folding] upon itself."[https://en.wikipedia.org/wiki/Reynolds_number#Object_in_a_fluid] (used under Creative Commons 2.0)]] | ||
Line 145: | Line 214: | ||
Okay, so what's happening here? Things look pretty "boring" so far. With the exception of the very first couple of frames, in which the fluid has not achieved its full velocity yet, all of the frames are visually nearly the same. As you can tell by the color scale on the velocity plot, the fluid is moving as fast as 2 m s<sup>-1</sup> past the cylinder, but there seems to be no instability here. This system is the result of '''kinematic''' forces at work, but the system seems to be stable, i.e. there is very little '''dynamic''' element to this system. Another way to say this is that there is not much variance in any given cell through time. | Okay, so what's happening here? Things look pretty "boring" so far. With the exception of the very first couple of frames, in which the fluid has not achieved its full velocity yet, all of the frames are visually nearly the same. As you can tell by the color scale on the velocity plot, the fluid is moving as fast as 2 m s<sup>-1</sup> past the cylinder, but there seems to be no instability here. This system is the result of '''kinematic''' forces at work, but the system seems to be stable, i.e. there is very little '''dynamic''' element to this system. Another way to say this is that there is not much variance in any given cell through time. | ||
− | Why is this? Well, we said before that honey is "sticky." In more technical terminology, higher viscosity means higher internal friction and resistance to deformation. This has the effect of dampening the inertial term in Navier-Stokes, and thus causes the flow to gain stability and to behave in a "boring," predictable manner. Take another look at the Reynolds number plot. All areas on the plot are '''''Re'' < 1'''. This indicates a very stable and predictable flow, in which the kinematics of any one particle anywhere in the continuum can be described quite well mathematically. | + | Why is this? Well, we said before that honey is "sticky." In more technical terminology, higher viscosity means higher internal friction and resistance to deformation. This has the effect of dampening the inertial term in Navier-Stokes, and thus causes the flow to gain stability and to behave in a "boring," predictable manner. Take another look at the Reynolds number plot. All areas on the plot are '''''Cell Re'' < 1'''. The overall ''Re'' is on the order of 10<sup>0.5</sup> (around 3.2) since velocity is 1.0 m/s, the linear dimension or cylinder width is 10<sup>-1</sup> m, and viscosity is 10<sup>1.5</sup> Pa s. This indicates a very stable and predictable flow, in which the kinematics of any one particle anywhere in the continuum can be described quite well mathematically. Let's take another look at the table we saw above: |
{| class="wikitable" style="text-align:center" | {| class="wikitable" style="text-align:center" | ||
Line 154: | Line 223: | ||
|Turbulent | |Turbulent | ||
|- | |- | ||
− | |''Re'' < | + | |''Re'' < 100 |
− | | | + | |100 < ''Re'' < 10<sup>5</sup> |
− | | | + | |10<sup>5</sup> < ''Re'' |
|} | |} | ||
− | Flows with Reynolds numbers of less than | + | Flows with Reynolds numbers of less than 100 are considered "laminar". This model shows laminar fluid flow around a cylinder. |
− | == Water (''μ'' = 10<sup>-3</sup> Pa s )== | + | == 2) Water (''μ'' = 10<sup>-3</sup> Pa s )== |
Now let's look at how flow changes when viscosity is lowered more than four orders of magnitude to that of water, ''μ'' = 10<sup>-3</sup> Pa s (remember, we're holding density constant). What do you think will be different? What do you think the system will look like? | Now let's look at how flow changes when viscosity is lowered more than four orders of magnitude to that of water, ''μ'' = 10<sup>-3</sup> Pa s (remember, we're holding density constant). What do you think will be different? What do you think the system will look like? | ||
− | === Velocity (x component) === | + | === Velocity 2 (x-component) === |
[[File:Mu10-3_ux1_velocity.gif]] | [[File:Mu10-3_ux1_velocity.gif]] | ||
− | Whoa! That's quite different. Notice that things initially begin laminar but start to decay into a regular pattern of "wobbling." This is called | + | Whoa! That's quite different. Notice that things initially begin laminar but start to decay into a regular pattern of "wobbling." This process of vortex formation in the wake of the flow around the cylinder is called [https://en.wikipedia.org/wiki/Vortex_shedding vortex shedding]. Notice also how violently the velocity vectors swing around as the vortices begin forming and shedding and the flow field oscillates from side to side. Flow is actually going backwards in some places! Why? |
There's no question this flow is more dynamic than the first one. Technically, as you'll see just below, this is still a laminar flow. Why? Can you still predict what's happening in certain places or at certain times? Why or why not? Keep these questions in mind as you scroll through the next few plots. | There's no question this flow is more dynamic than the first one. Technically, as you'll see just below, this is still a laminar flow. Why? Can you still predict what's happening in certain places or at certain times? Why or why not? Keep these questions in mind as you scroll through the next few plots. | ||
− | === Shear rate === | + | === Shear rate 2 === |
[[File:Mu10-3 ux1 shear.gif]] | [[File:Mu10-3 ux1 shear.gif]] | ||
Here we see the shear plot, which still tracks the derivative of the velocity field, but in this case it's much more dynamic as well. We can see the formation of vortices as the dominant shear jumps back and forth between the two sides of the cylinder. Why do you think this is happening? | Here we see the shear plot, which still tracks the derivative of the velocity field, but in this case it's much more dynamic as well. We can see the formation of vortices as the dominant shear jumps back and forth between the two sides of the cylinder. Why do you think this is happening? | ||
− | === Vorticity magnitude === | + | === Vorticity magnitude 2 === |
[[File:Mu10-3 ux1 vorticity.gif]] | [[File:Mu10-3 ux1 vorticity.gif]] | ||
− | What a gorgeous vorticity plot. After you've admired it for a bit, can you describe what's happening here? Look back at the shear plot. When the newest vortex is about to detach from the lee of the cylinder, where is the shear rate highest? | + | What a gorgeous vorticity plot. After you've admired it for a bit, can you describe what's happening here? Look back at the shear plot. When the newest vortex is about to detach from the [https://en.wikipedia.org/wiki/Windward_and_leeward lee side] of the cylinder, where is the shear rate highest? |
− | === Pressure === | + | === Pressure 2 === |
[[File:Mu10-3 ux1 pressure.gif]] | [[File:Mu10-3 ux1 pressure.gif]] | ||
− | Look at the similarities between this pressure plot and the vorticity plot, and you'll notice that pressure is inversely related to vorticity. Why? Can you think of real-life scenarios (other than flow past a cylinder in a flume) where you can observe this phenomenon? Recall the flow vectors going backwards. Given this pressure plot, can you give an explanation for this phenomenon? | + | Look at the similarities between this pressure plot and the vorticity plot, and you'll notice that pressure is more or less inversely related to vorticity after the fluid passes the cylinder. Why? Can you think of real-life scenarios (other than flow past a cylinder in a flume) where you can observe this phenomenon? Recall the flow vectors going backwards. Given this pressure plot, can you give an explanation for this phenomenon? |
− | === Reynolds number === | + | === Reynolds number 2 === |
[[File:Mu10-3 ux1 reynolds.gif]] | [[File:Mu10-3 ux1 reynolds.gif]] | ||
− | + | Notice the change in magnitude of the cell Reynolds numbers calculated in this model. Recall that higher Reynolds numbers suggest more turbulent flow while lower Reynolds numbers indicate more laminar flow. Where do you see the most turbulent flow in the model? The least? Why do you think this is happening? | |
+ | |||
+ | The overall Reynolds number for the system is 89. The Reynolds number doesn't quite make it above the critical number of 100 in order to be considered a "transitional" flow. What is happening in this flow that keeps it relatively "predictable?" | ||
+ | |||
+ | ''Note: The stippling is an artifact of the meshing process in COMSOL.'' | ||
+ | |||
+ | === Discussion 2 - Water === | ||
+ | |||
+ | The vortex shedding pattern shown in these examples develops after a couple of brief moments in which the flow is fairly laminar and there are few dynamics acting on the system. Then the system begins to develop an instability. In real life this instability is the result of tiny perturbations on the surface of the cylinder that cause differences in the boundary layer thickness as flow passes, causing one side to briefly slip faster than the other. The momentum of the vortex continues over to the other side of the cylinder, which increases the fluid pressure on that side and thus slows flow. As pressure always wants to equilibrate, this process reverses and a competing vortex is sent spinning to the opposite side. If flow conditions do not change, this process will continue indefinitely. | ||
+ | |||
+ | In mathematical terms, fluid particles will accelerate over time—'''∂v / ∂t'''—towards areas of low pressure—'''- ∇P''' (or decelerate if they are already traveling away from an area of low pressure). In order to figure out whether a particular particle will accelerate (or decelerate) towards a certain area of pressure, you'd have to examine the direction magnitude component partial differentials of the velocity and term, '''∇<sup>2</sup>U'''. In other words, the ''grad'' ('''∇''') symbol is a shorthand for the fact that you're looking at something that changes in more than one linear dimension (in the case of this simple 2D model, '''∇''' denotes that the variable will change in both ''x'' and ''y''). | ||
+ | |||
+ | In a 3D model, the same patterns hold true. Let's look at a particle model of the same process. The SPH-generated models below (and all others in this module) show the motion of ~10<sup>5</sup> particles. Particles in the first plot here are given colors based on the ''x'' component of their velocity. | ||
+ | |||
+ | [[File:2019-03-01-Water_VelX.gif]] | ||
+ | |||
+ | In the second plot, particles are given colors based on their vorticity. | ||
− | + | [[File:2019-03-01-Water Vort VelMagVectors.gif]] | |
− | + | As a fluid becomes less viscous, the momentum term will begin to dominate the Navier-Stokes solution, meaning that the internal shear strength of the fluid is less able to keep it from deforming. As we said before, in this ''flow past a cylinder'' model, that means vortex shedding will become more and more viable at either lower viscosities or higher velocities. | |
− | + | === Real-world applications 2 === | |
[[File:Transitional.jpg|thumb|Quasi-laminar flow past a cylinder (a GPS survey staff) on Third River in Montclair, NJ. (Photo: Ian Nesbitt, licensed under Creative Commons 4.0)]] | [[File:Transitional.jpg|thumb|Quasi-laminar flow past a cylinder (a GPS survey staff) on Third River in Montclair, NJ. (Photo: Ian Nesbitt, licensed under Creative Commons 4.0)]] | ||
− | + | Pictured at right, a GPS survey staff causes a slight flow instability downstream. | |
+ | |||
+ | As beautiful as they are, von Kármán vortex streets are an engineering problem in many real-world applications. Vortex shedding can put enormous shear forces on mechanical joints, which can suffer brittle failure. | ||
+ | |||
+ | [[File:Mount-shear.jpg|200px|A survey mount with the Z-joint shorn off.]] | ||
+ | [[File:Mount-shear-zjoint.jpg|632px|A survey mount with the Z-joint shorn off.]] | ||
+ | |||
+ | The photos above show a weld joint that has failed due to shear forces caused by vortex shedding. At the time of failure, the vessel was traveling about 2-2.5 m/s. Luckily, the mount was secured with rope and the instrument was not lost. | ||
+ | |||
+ | Low pressure behind a cylindrical marine survey mount pole can cause approximately an order of magnitude more drag than a hydrodynamic shape like a teardrop, even at low speeds. Stainless steel "fairings" are sometimes used to reduce this drag and stop the pole from flexing normal (perpendicular) to the direction of travel. Think back to the vorticity and pressure plots from the flow past a cylinder model above. Can you explain why a teardrop-shaped mount would result in more stable flow? | ||
+ | |||
+ | [[File:ADCPfairing.JPG|A fairing sheath used to reduce drag on a survey mount pole.]] | ||
+ | [[File:ADCPfairing_operation.JPG|Fairing sheath in action. Note teardrop shape, meant to reduce pressure instability behind survey mount pole.]] | ||
+ | |||
+ | |||
+ | Below are velocity, shear rate, vorticity, Reynolds number, and pressure plots generated in COMSOL for the same fluid flowing around a teardrop-shaped object instead of the cylinder. Compare these to the plots shown above for the cylindrical impediment. You may still notice signs of oscillating flow resulting from the disturbance, but flow is ''much'' more laminar. Can you explain why this might be? | ||
+ | |||
+ | [[File:fairing_water_velocity.gif]] | ||
+ | |||
+ | Pay attention especially to how the velocity vectors change (or do not change) throughout time. Compare this to the velocity from the water model with the cylindrical impediment. What does this indicate about the differences in inertial forces between the two scenarios? | ||
+ | |||
+ | [[File:fairing_water_shear.gif]] | ||
+ | |||
+ | [[File:fairing_water_vorticity.gif]] | ||
+ | |||
+ | This looks vastly different from the vorticity plot for the cylinder model. | ||
+ | |||
+ | [[File:fairing_water_reynolds.gif]] | ||
+ | |||
+ | Note how much lower the cell Reynolds number is compared to the cylinder model! | ||
+ | |||
+ | [[File:fairing_water_pressure.gif]] | ||
+ | |||
+ | This also looks vastly different from the pressure plot for the cylinder model. It's amazing how such a simple design can result in a major shift in flow around the object. | ||
+ | How does the teardrop shape influence the pressure and vorticity? | ||
− | |||
− | === Velocity (x component) === | + | Now, let's take a look at this behavior in a fluid with two orders of magnitude less viscosity than water: air. |
+ | |||
+ | ==3) Air (''μ'' = 10<sup>-5</sup> Pa s)== | ||
+ | |||
+ | Air has a viscosity of ''μ'' = 10<sup>-5</sup> Pa s (still holding density and velocity constant). How do you think this will affect the deformation of the fluid? | ||
+ | |||
+ | === Velocity (x-component) 3 === | ||
[[File:Mu10-5_ux1_velocity.gif]] | [[File:Mu10-5_ux1_velocity.gif]] | ||
− | === Shear rate === | + | Compare this velocity plot to the velocity from scenario 2 (Water). The initial velocity of the fluid is the same for both scenarios. Why might the maximum velocity be higher for one versus the other? |
+ | |||
+ | Note: The scale bar is different between the two. | ||
+ | |||
+ | === Shear rate 3 === | ||
[[File:Mu10-5 ux1 shear.gif]] | [[File:Mu10-5 ux1 shear.gif]] | ||
− | === Vorticity magnitude === | + | Compare this shear rate plot with [[Fluid Flow Past a Cylinder#Shear rate 2|the one above]]. Why is this one "sharper," i.e. the velocity gradient is more severe across the shear zone? What about air in comparison to water allows that to happen? |
+ | |||
+ | === Vorticity magnitude 3 === | ||
[[File:Mu10-5 ux1 vorticity.gif]] | [[File:Mu10-5 ux1 vorticity.gif]] | ||
− | + | What is happening to the vorticity as the fluid moves further past the cylinder? Energy from the disturbance propagates forward and eventually dissipates. Can you see where this is happening from each of other variable plots as well? | |
− | === Pressure === | + | === Pressure 3 === |
[[File:Mu10-5 ux1 pressure.gif]] | [[File:Mu10-5 ux1 pressure.gif]] | ||
− | === Reynolds number === | + | In this plot, pressure is not only oscillating back and forth upstream of the cylinder, it seems to be oscillating in the channel behind it as well. Pressure oscillations that occur under these fluid conditions may be occurring near what's called a [https://en.wikipedia.org/wiki/Resonance resonant frequency] for this channel. |
+ | |||
+ | === Reynolds number 3 === | ||
[[File:Mu10-5 ux1 reynolds.gif]] | [[File:Mu10-5 ux1 reynolds.gif]] | ||
− | The stippling is an artifact of the meshing process in COMSOL. | + | These cell Reynolds numbers are several orders of magnitude higher than those calculated for the water scenario. In this case, the Reynolds number is above the critical number of 100, which makes it a "transitional" flow. In the range of transitional Reynolds numbers, 100 to 10<sup>5</sup>, eddy-like vortices begin to form and propagate downstream. This phenomenon is much easier to visualize using a 3D particle solution. Let's look at the SPH models for this scenario. |
+ | |||
+ | Note: The stippling is an artifact of the meshing process in COMSOL. | ||
+ | |||
+ | === Discussion 3 - Air === | ||
+ | |||
+ | This specific type of oscillating flow is called a [https://en.wikipedia.org/wiki/K%C3%A1rm%C3%A1n_vortex_street von Kármán vortex street] (VKVS), named after [https://en.wikipedia.org/wiki/Theodore_von_K%C3%A1rm%C3%A1n Theodore von Kármán], the Hungarian-American physicist who first described it in detail. The process that leads to this type of flow is called [https://en.wikipedia.org/wiki/Vortex_shedding vortex shedding]. Let's take a deeper look at how these vortices are forming by looking at the particle solution generated in SPH. | ||
+ | |||
+ | |||
+ | [[File:2019-03-02-Air_VelX.gif]] | ||
+ | |||
+ | |||
+ | |||
+ | [[File:2019-03-02-Air Vort VelMagVectors.gif]] | ||
+ | |||
+ | These von Kármán vortex streets refer to the double row of vortices being shed from either side of the cylinder. The vortices formed from one side rotate in the opposite direction as the vortices formed from the other side. Each respective vortex row is referred to as a vortex street. Notice that angles at which the vortexes are moving relative to each other. | ||
+ | |||
+ | Compare the vortices here to those generated in the water flow around a cylinder model. What stands out to you about these vortices and what do you think is causing those differences? The ability of these vortices to maintain their form and stability through the entire simulation is remarkable. What do you notice about how they change over time and space? You may notice that these vortices are spaced differently and that they are different sizes than those from the water flow model. These VKVS can be described using several parameters: | ||
+ | |||
+ | The geometry of a VKVS can be defined by two dimensionless ratios, their '''aspect ratio''' and their '''dimensionless width'''. The aspect ratio is equal to '''h/a''' where h is equal to the separation distance between 2 the counter-rotating vortex streets and a is the the distance between 2 vortices in the same vortex street. What would you estimate this ratio to be for the vortices above? The dimensionless width of the VKVS is '''h/D''' where D is the diameter of the obstacle (cylinder in this case). In other words, the dimensionless width is just the ratio of the vortex street width to the width of the obstacle. What would you estimate the dimensionless width to be for the vortex street above? These parameters allow us to compare the geometry of vortex streets that vary vastly in size scale. The stable aspect ratio and dimensionless widths observed in lab settings are 0.28 and 1.2, respectively. How do these compare to those you calculated for this VKVS? | ||
+ | |||
+ | The vortex shedding frequency of a VKVS can be calculated from its [https://en.wikipedia.org/wiki/Strouhal_number Strouhal number], which describes the periodicity of oscillating flow mechanisms. The Strouhal number (St) is calculated using the frequency of vortex shedding (f), the obstacle/object diameter (D), and the flow velocity (u): '''St = f*D/u'''. Knowing the cylinder diameter (0.1 m) and the flow velocity (1.0 m/s), can you count the vortex shedding frequency from the animation to calculate the Strouhal number of this VKVS? | ||
+ | |||
+ | These von Kármán vortex streets are well-studied fluid phenomena that occur during the transition to turbulence (when 100 < Re < 10<sup>5</sup>). Vortex shedding has many real-world engineering and design applications, some of which were described in the water flow discussion. Next, let's learn about their atmospheric counterparts! | ||
+ | |||
+ | === Real-world applications 3 === | ||
+ | |||
+ | ==== Atmospheric instability ==== | ||
+ | |||
+ | [[File:canaryIslands_tmo_2015140.jpg|thumb|900px|right|View of atmospheric VKVS off of Madeira and the Canary Islands on May 20, 2015 from the NASA TerraX Satellite.]] | ||
+ | |||
+ | Kármán vortex streets have been thoroughly-modeled in lab settings, but they occur naturally more often than you might think. In fact, the first VKVS described by Theodore von Kármán were observed in the sky. He noticed remarkable swirling patterns in the clouds forming on the lee side of an island. These VKVS occur on a much larger scale than the VKVS that are modeled in lab settings. In the case of these atmospheric vortex streets, there are vertical forces, atmospheric pressure and temperature gradients, and a whole slough of other factors that influence the geometry and stability of the vortices. Many studies have modeled atmospheric VKVS such as the ones shown in the image to the right. | ||
+ | |||
+ | In the case of these atmospheric VKVS, the island acts as the cylinder in our fluid flow models, creating the flow disturbance. As air flows around the island obstacle, vortex shedding begins and these counter-rotating vortices propagate downwind. Do you notice any other differences between these atmospheric VKVS and the simulated VKVS from our air flow around a cylinder model? | ||
+ | |||
+ | Using the scale bar in the image, measure the linear dimension (D) or width of Madeira. Using a wind speed of 10 m/s and the viscosity of air, can you calculate the general Reynolds number for flow around Madeira using the same steps as you previously did in the module? | ||
+ | |||
+ | Now use the same scale bar to measure and characterize the geometry of these atmospheric VKVS. What's the aspect ratio of the VKVS created by Madeira? The dimensionless width? How do these compare to those values observed in lab settings? | ||
+ | |||
+ | ==== Truck tail fairings ==== | ||
+ | |||
+ | Have you ever gotten a little too close to the back of a tractor trailer on the highway and noticed that your car was being buffetted around side-to-side in the wind? If so, you have experienced the effects of von Kármán vortex streets firsthand. | ||
+ | |||
+ | If you've ever seen a tractor trailer with panels hanging off its tail (see image below), you've also seen strategies to counter the effects of vortex shedding firsthand. Remember the marine survey mount fairings from [[Fluid Flow Past a Cylinder#Real-world applications 2|the previous Real-world applications section]]? These trailer fairings serve essentially the same purpose: reducing drag and causing a more aerodynamic slipstream. The following image is an example of a commercial application of fluid dynamics. | ||
+ | |||
+ | [[File:Tail fairings.jpg|Fluid dynamics being sold to consumers!]] | ||
+ | [[File:Atdynamics trailertail.jpg|Fluid dynamics being sold to consumers!]] | ||
+ | |||
+ | This image shows the effects of creating a more efficient slipstream which reduces vortex shedding and improves fuel efficiency. One estimate claims [https://slate.com/culture/2013/04/truck-panels-what-do-they-do-explained-photos.html] that these tail fairings can increase fuel efficiency by approximately 10% over hauling distances. Have you thought about why this works? What about the truck and survey pole fairings decreases that instability and allows less vortex shedding? | ||
+ | = Conclusions = | ||
− | + | This module has walked you through various stages in the transition to turbulence. Can you describe this transition in your own words? We have shown you fluid systems with varying levels of predictability. In addition, this module introduced you to some of the tools that you can use to qualitatively and quantitatively characterize fluid flow as well as the physics behind it. The Navier-Stokes momentum equation governs the fluid particle motion while the Reynolds number describes the flow regime. The von Kármán vortex streets generated in transitional flows can also be characterized by their aspect ratio, dimensionless width, and vortex shedding frequency (Strouhal number). Now that you have explored the transition to turbulence through models of fluid flow around a cylinder, you can use your knowledge to examine turbulence and flow behavior in other fluid systems! | |
− | = Complex | + | = Bonus: Complex flows = |
− | Although our models | + | Although our module focused on models of simple fluid flow, more complex flows make up the vast majority of flow behavior you'll encounter in the real world. It's important to note that the systems modeled above above are highly simplified in order to highlight the physical forces acting on fluids. Below are some examples of more complex flow systems that one might encounter in the real world. |
== Fully turbulent flows == | == Fully turbulent flows == | ||
− | [[File:Turbulent.jpg|thumb| | + | [[File:Turbulent.jpg|thumb|600px|Even at low flow, a US Army Corps of Engineers flood control project on the Hoosac River in North Adams, Massachusetts causes a brief transition from laminar to turbulent flow. Photo was taken four years to the day after Hurricane Irene (see GIF, left), the flood of record at USGS gaging station [https://waterdata.usgs.gov/nwis/uv/?site_no=01332500 01332500] (gaging station is green shed with solar panel in this photo). (Photo: Ian Nesbitt, August 28, 2015, licensed under Creative Commons 4.0)]] |
− | Fully turbulent flow, where ''' | + | Fully turbulent flow, where '''10<sup>5</sup> < Re''' and predictability over a scale larger than a couple of particles or beyond a couple of time steps approaches zero, is very difficult to model. In some cases, flows of this nature are easier to compute and the solutions are better represented by [[Smoothed Particle Hydrodynamics|Smoothed Particle Hydrodynamic]] models, in which individual particle smoothing kernels, rather than mesh elements, define the behavior of the fluid. However, flows in high Reynolds cases are are difficult to describe mathematically, and thus solutions that approach full turbulence in continuum or smoothed particle models can take orders of magnitude longer to compute. |
− | [[File:Fullturbulence.gif|(Hurricane Irene flood GIF: Ian Nesbitt, licensed under Creative Commons 4.0)]] | + | [[File:Fullturbulence.gif|400px|(Hurricane Irene flood GIF: Ian Nesbitt, licensed under Creative Commons 4.0)]] |
− | The gif above was filmed on August 28, 2011, near peak flow during Hurricane Irene, the current flood of record for USGS gaging station [https://waterdata.usgs.gov/nwis/uv/?site_no=01332500 01332500] near Williamstown, MA. The video shows flow over a US Army Corps of Engineers (USACE) flood control structure (also pictured at baseflow on right). The concrete-bedded flood control flume has low bed roughness and thus high velocity, and comparatively lower ''Re''. Flows like this can be very erosive when they encounter a jump in bed roughness due to a transition from a flood-control flume with a concrete bed to natural (rougher) bed conditions. The purpose of induced turbulence—from USACE's perspective—is to limit scour caused by a sudden increase in bed roughness. By reducing friction at the boundary layer, the flow will not be quite as erosive in its transition between bed conditions. | + | The gif above was filmed on August 28, 2011, near peak flow during Hurricane Irene, the current flood of record for USGS gaging station [https://waterdata.usgs.gov/nwis/uv/?site_no=01332500 01332500] near Williamstown, MA. The video shows flow over a US Army Corps of Engineers (USACE) flood control structure (also pictured at baseflow on right). The concrete-bedded flood control flume has low bed roughness and thus high velocity, and comparatively lower ''Re''. Flows like this can be very erosive when they encounter a jump in bed roughness due to a transition from a flood-control flume with a concrete bed to natural (rougher) bed conditions. The purpose of induced turbulence—from USACE's perspective—is to limit scour caused by a sudden increase in bed roughness. By increasing turbulence and thereby reducing friction at the boundary layer, the flow will not be quite as erosive in its transition between bed conditions. The flow captured in this video is at or near the flood control project's design capacity to limit the destructive nature of the flow, and thus this event still eroded cobble- and boulder-sized particles from the natural bed. |
== "Multiphase" flows == | == "Multiphase" flows == |
Latest revision as of 20:04, 15 May 2019
Created by Ian Nesbitt and Jukes Liu on 2019-02-19. Because this page has some high-resolution animations, it is best viewed on a reliable internet connection.
Welcome to our teaching module exploring the transition to turbulence through models of fluid flow around a cylinder!
Transitioning to turbulence involves decreasing the predictability of a system. Inertial forces begin to dominate over viscous forces, resulting in more chaotic particle motion in the system (take a quick look at the Hurricane Irene example below in the Complex Flow section). In this module, we will explore this transition and learn how viscosity affects the dynamics of a fluid flowing around a cylindrical impediment. We can observe an interesting phenomenon called Von Kármán Vortex Streets at this simulated transition to turbulence. These naturally-occurring phenomena are fascinating and have many natural and engineering implications. By the end of the module, you should be able to describe what's occurring in each of the scenarios presented and have a good grasp on the dynamics involved in the complex flow examples. You will be able to describe the initial conditions of a system, the transition from laminar to turbulent flow, and the effect viscosity has on the inertia, complexity, and predictability of a system!
Below is a snapshot of one of our computational models of water flowing past a cylinder. In this early time-step, we can see an instability begin to develop in the wake of the cylinder.
Here is a satellite loop of a von Karman Vortex Street developing in the wake of Guadalupe Island off the coast of Baja California, Mexico. (source: twitter user @weatherdak)
Overview
In order to model the transition to turbulence and the effects of changing viscosity on the dynamics of a simple fluid system with a single cylindrical impediment placed in the flow path, we use several modeling tools: COMSOL Multiphysics, Smoothed-Particle Hydrodynamics (SPH), and ParaView. We will describe the model set-up and its physical basis, the differences between the three scenarios with fluids of different viscosities, and several real-world implications. We will move from looking at the behavior of more viscous fluids and move towards fluids with lower viscosities. Note: Viscosity is defined as the measure of a fluid's resistance to deformation.
First, let's start by learning how to talk about the various components of flow.
Characterizing the fluid dynamics
When we talk about fluid flow, we need to first describe the fluid. Some of the fundamental characteristics of fluid are density, viscosity, compressibility, heat capacity, and thermal conductivity. In this exercise we will ignore the thermal properties entirely, define a constant density and compressibility, and focus most of our attention on how viscosity affects the kinematics of a fluid system.
Compressibility and density are fairly easy to define. Compressibility is the tendency of a fluid to change its volume due to changes in pressure. Since we are not dealing with immense pressure, we assume that compressibility is zero across all models. Density is the quantity of mass per unit volume. For the purposes of this model, we will hold density constant at 1 kg m-3 (approximately that of freshwater) to try and isolate the effects of viscosity. These parameters will be fed into the Navier-Stokes fluid momentum equation (below) for each location in the model at each time step.
To characterize the motion of particles in the fluid, we must account for the changes in momentum. This Navier-Stokes equation is derived based on the conservation of momentum in a system. It is the foundation of our models. This equation can be broken down into its different terms, which represent the effects of the inertial forces, body forces, viscous forces, and the pressure gradient throughout the system.
This is the basic structure of the Navier-Stokes momentum equation:
Mass * acceleration = Body forces + Shear forces - Pressure gradient
These qualitative terms are represented by some greek symbols which may or may not mean anything to you right now, but we'll break them down for you.
ρ (∂v / ∂t) = Δρg + µ∇2U - ∇P
where | |
---|---|
∂v | = change in velocity |
∂t | = change in time |
ρ | = density |
g | = acceleration due to gravity |
µ | = viscosity |
∇2U | = curvature of velocity field (2nd derivative) |
∇P | = divergence of pressure (gradient) |
The inertial forces (acceleration) is represented by ∂v / ∂t.
On the right hand side of the equation, we have the body forces from density and gravity (ρg), viscous forces from the viscosity property of the fluid (µ∇2U), and the pressure gradient throughout the system (∇P). Each of these forces will influence the acceleration or motion of particles. Can you visualize how these different forces on the right-hand side of the equation might influence a particle's motion?
Solving this equation for each grid point or particle at each time step will define how our fluid will behave in a computational sense. Once our fluid starts to move, we need ways to describe how it is flowing. Fluid flow can be characterized as either laminar or turbulent, which has to do with the predictability of its motion throughout the system. The parameter that is used to describe this characteristic is called the Reynolds number.
Reynolds number and things that affect it
The Reynolds number, Re, is a dimensionless number that represents the flow regime of a fluid. The Reynolds number is a way of representing whether a flow is laminar, transitional, or fully turbulent using numerical values. When flow is laminar, the fluid motion is more uni-directional, smooth, and more predictable. Imagine the flow of molasses being poured out onto a table. Another example would be toothpaste being squeezed out of the tube. Laminar flow is represented by lower Reynolds numbers. When flow is turbulent, fluid motion is more irregular. A gust of wind flowing around a flag-pole causing the flag to flap behind it is an every-day example of a more turbulent flow. These flows are characterized by higher Reynolds numbers.
What are some other real-world examples of fluid flow that you can think of? Would you characterize the flow as more laminar or turbulent?
Viscosity
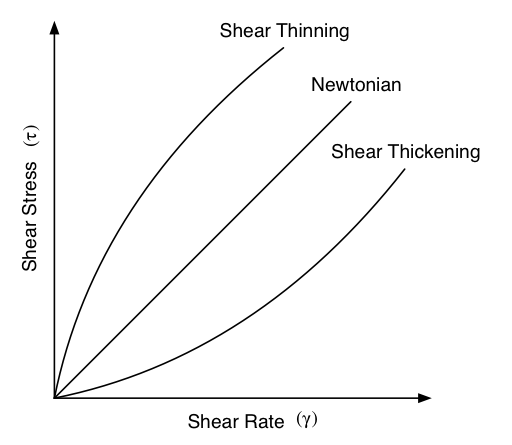
Keeping those real-world examples in mind, we can brainstorm about the differences in those fluid systems that might affect the flow pattern. There are differences in the fluid properties between the molasses, toothpaste, and atmospheric air. Once of the main differences, which we examine in depth in this module, is their difference in viscosity. "Viscosity" is a term you might be familiar with in terms of describing a fluid. The technical definition of viscosity is a fluid's capability of resisting deformation. Molasses and toothpaste are more viscous than water, which means that their flow is more difficult to deform or disturb. Meanwhile, air has a much lower viscosity and is quite easily deformed! We deform air every time we move. Therefore, if everything else is held constant, increasing viscosity decreases the Reynolds number which means that fluid flow becomes more laminar. If we decrease viscosity, fluid flow will begin to transition towards turbulence.
The conceptual diagram at right shows viscous regimes. A fluid that exhibits a linear relationship between stress and strain is described as Newtonian. Any force that is applied to Newtonian fluids results in a proportional amount of deformation. Shear thickening is a term used to describe a nonlinear regime in which greater force can result in less deformation (corn starch and water, for example...watch a very British demonstration of this behavior here). Conversely, shear thinning describes a fluid that deforms more easily with increased force (think about paint - it runs readily when applied with a brush or roller, yet just moments after retains enough viscosity to stay in place with minimal running).
Velocity
Another main parameter that influences the flow regime is the velocity of the fluid. Faster-flowing fluids tend to result in more turbulent responses. In the air around a flagpole example, higher wind velocity will result in a more turbulent response which one would observe as more violent "flapping".
Therefore, Reynolds number is a function of viscosity and velocity: f(µ, v). Velocity and viscosity have inverse influences on the Reynolds number (i.e. as velocity increases, the Reynolds number increases while increasing viscosity lowers the Reynolds number). This module will walk you through the transitions that occur when we decrease viscosity while holding everything else, including velocity, constant. We are choosing to focus on examining the effects of lowering viscosity by examining fluid flow fluids with different viscosities (honey, water, air) while holding the velocity constant. This would have a similar effect as increasing velocity and holding viscosity constant. Using our models, we examine the effects of changing viscosity, effectively changing the Reynolds number, on fluid flow.
As we have introduced above, the Reynolds number is an extremely useful way to characterize flow conditions. The Re number is equal to the inertial forces (velocity times characteristic length) over the resisting forces (viscosity).
Re = ρVD/µ = VD/v
where | |
---|---|
V | = fluid velocity (m s-1) |
D | = linear dimension (m) |
µ | = dynamic viscosity (Pa s) |
v | = kinematic viscosity (Pa s) |
ρ | = density (kg/m3) |
Note: Re can also be thought of as inversely related to how well flow conditions can be described mathematically across a given dimension (x, y, z, or time).
The table below lists the qualitative descriptions for each quantitative Re range.
Quantifying qualitative descriptions of Reynolds number | ||
---|---|---|
Laminar | Transitional | Turbulent |
Re < 100 | 100 < Re < 105 | 105< Re |
Flows with Reynolds numbers of less than 100 are considered "laminar," while those from 100 to 105 are "transitional," and above 105 are "turbulent." At low Reynolds numbers (Re < 100), viscous forces dominate and flow is laminar. As the Reynolds number increases, due to lower velocity or higher viscosity, inertial forces begin to play a greater role and flow becomes increasingly turbulent. In this transition between laminar and turbulent flow, we begin to observe some unique fluid phenomena. Let's first describe our model and then take a look at these phenomena!
Model setup
Geometry
Below is the geometry of our simple model for fluid flow described by Navier Stokes equation (above) and solved as a finite-element model with help from numerical methods of COMSOL.
This is a two-dimensional COMSOL model, which assumes that the horizontal (long) walls and the walls of the cylinder have a "no slip" condition. This means that as the flow gets closer to the wall, velocity goes to zero. This condition sets up a velocity gradient (shear) between the walls at zero and the center of the flow. The wall on the far left side has an inflow condition of 1 meter per second, and the wall on the right side has a zero-pressure outlet condition, which lets flow pass out of the model unhindered.
COMSOL solves a finite element model, which means that it performs calculations for a mesh grid at each step. We use a relatively small mesh cell size ("Extra Fine" setting in COMSOL) on the order of ~1 cm.
When we run the model, we are executing a variation of the Navier-Stokes momentum equation for each mesh element of the model at each time step. This equation, shown above, is fundamental to describing the behavior of fluids in continuum mechanics.
Experimental variable: Viscosity
Let's look at the dynamic viscosities of fluids we'll be working with.
Fluid | µ (viscosity at 20 ºC) |
---|---|
1. Honey | 1 * 101.5 Pa s |
2. Water | 0.89 * 10-3 Pa s |
3. Air | 1.81 * 10-5 Pa s |
As mentioned above, we use an initial fluid velocity of 1 m/s in all of our models.
Questions to consider
From the diagram of the model geometry, what is the linear dimension (D)? In this model, it is equivalent to the diameter of the cylinder.
Before we go through the model results, try calculating the initial Reynolds numbers for each fluid viscosity using the linear dimension and the fluid velocity. Based on the Reynolds number calculated for the honey, do you think the fluid flow will be more laminar or turbulent? What about for water? Air?
Models
1) Honey (μ = 101.5 Pa s)
In the first example, we have a fluid with the viscosity of about that of honey, μ = 101.5 Pascal seconds (Pa s). You might imagine honey to be a pretty "stiff" liquid, which has something to do with its viscosity. What do you think will happen? Let's look at a few parameters of flow in the honey model.
Velocity 1 (x-component)
Things are pretty orderly and logical here. Not a whole lot changes over time. You might describe this flow system as "laminar," since you can describe what will happen at any given point in the model space at any given time fairly easily. Note that velocity is highest near the cylinder where the honey must "squeeze by" the cylinder in order to keep up with the 1 m s-1 inflow rate. This sets up a steep velocity gradient near the no-slip boundary of the cylinder, which we can see in the shear rate:
Shear rate 1
Shear rate is by definition the derivative of the velocity field, so it is no surprise that the highest shear values are in the areas next to the cylinder where the steep velocity gradient exists. If we break shear down into its component parts, we get vorticity. Vorticity is the curl of the velocity field, or in other words, the rate of rotation of the angle between two particles as they slip past each other.
Vorticity 1
Again, unsurprisingly, the curl is highest where the gradient of velocity is high. This makes sense because as two particles slip past each other at different velocities, their orientation changes (rotates) with regards to one another. Vorticity will be highest near the no-slip boundaries in a simple laminar system like this.
Pressure 1
The pressure field should also make sense, because our one obstacle in this model sets up the overall gradient from inflow to outflow pretty nicely. Notice that the pressure values are very slightly higher on the stoss side and slightly lower on the lee side of the cylinder. Note also that pressure gradients define the shortening and stretching of a system. Flow is shortened as it is forced towards the front of the cylinder and stretched as it goes past the cylinder.
Reynolds number 1
Reynolds number describes how chaotic a system is. Since our system has almost no chaos, this plot is pretty boring at this viscosity.
You may have noticed that the Reynolds numbers shown here are different orders of magnitude than those you calculated earlier. That's because the Reynolds numbers calculated via COMSOL are cell Reynolds numbers. This means that the Reynolds number is calculated using the characteristic length scale of the mesh grid size rather than the whole system. Despite this distinction, examining relative Reynolds numbers throughout the model will be useful for qualitatively describing what's happening with the flow.
Discussion 1 - Honey
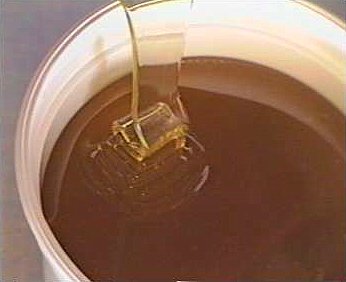
Okay, so what's happening here? Things look pretty "boring" so far. With the exception of the very first couple of frames, in which the fluid has not achieved its full velocity yet, all of the frames are visually nearly the same. As you can tell by the color scale on the velocity plot, the fluid is moving as fast as 2 m s-1 past the cylinder, but there seems to be no instability here. This system is the result of kinematic forces at work, but the system seems to be stable, i.e. there is very little dynamic element to this system. Another way to say this is that there is not much variance in any given cell through time.
Why is this? Well, we said before that honey is "sticky." In more technical terminology, higher viscosity means higher internal friction and resistance to deformation. This has the effect of dampening the inertial term in Navier-Stokes, and thus causes the flow to gain stability and to behave in a "boring," predictable manner. Take another look at the Reynolds number plot. All areas on the plot are Cell Re < 1. The overall Re is on the order of 100.5 (around 3.2) since velocity is 1.0 m/s, the linear dimension or cylinder width is 10-1 m, and viscosity is 101.5 Pa s. This indicates a very stable and predictable flow, in which the kinematics of any one particle anywhere in the continuum can be described quite well mathematically. Let's take another look at the table we saw above:
Quantifying qualitative descriptions of Reynolds number | ||
---|---|---|
Laminar | Transitional | Turbulent |
Re < 100 | 100 < Re < 105 | 105 < Re |
Flows with Reynolds numbers of less than 100 are considered "laminar". This model shows laminar fluid flow around a cylinder.
2) Water (μ = 10-3 Pa s )
Now let's look at how flow changes when viscosity is lowered more than four orders of magnitude to that of water, μ = 10-3 Pa s (remember, we're holding density constant). What do you think will be different? What do you think the system will look like?
Velocity 2 (x-component)
Whoa! That's quite different. Notice that things initially begin laminar but start to decay into a regular pattern of "wobbling." This process of vortex formation in the wake of the flow around the cylinder is called vortex shedding. Notice also how violently the velocity vectors swing around as the vortices begin forming and shedding and the flow field oscillates from side to side. Flow is actually going backwards in some places! Why?
There's no question this flow is more dynamic than the first one. Technically, as you'll see just below, this is still a laminar flow. Why? Can you still predict what's happening in certain places or at certain times? Why or why not? Keep these questions in mind as you scroll through the next few plots.
Shear rate 2
Here we see the shear plot, which still tracks the derivative of the velocity field, but in this case it's much more dynamic as well. We can see the formation of vortices as the dominant shear jumps back and forth between the two sides of the cylinder. Why do you think this is happening?
Vorticity magnitude 2
What a gorgeous vorticity plot. After you've admired it for a bit, can you describe what's happening here? Look back at the shear plot. When the newest vortex is about to detach from the lee side of the cylinder, where is the shear rate highest?
Pressure 2
Look at the similarities between this pressure plot and the vorticity plot, and you'll notice that pressure is more or less inversely related to vorticity after the fluid passes the cylinder. Why? Can you think of real-life scenarios (other than flow past a cylinder in a flume) where you can observe this phenomenon? Recall the flow vectors going backwards. Given this pressure plot, can you give an explanation for this phenomenon?
Reynolds number 2
Notice the change in magnitude of the cell Reynolds numbers calculated in this model. Recall that higher Reynolds numbers suggest more turbulent flow while lower Reynolds numbers indicate more laminar flow. Where do you see the most turbulent flow in the model? The least? Why do you think this is happening?
The overall Reynolds number for the system is 89. The Reynolds number doesn't quite make it above the critical number of 100 in order to be considered a "transitional" flow. What is happening in this flow that keeps it relatively "predictable?"
Note: The stippling is an artifact of the meshing process in COMSOL.
Discussion 2 - Water
The vortex shedding pattern shown in these examples develops after a couple of brief moments in which the flow is fairly laminar and there are few dynamics acting on the system. Then the system begins to develop an instability. In real life this instability is the result of tiny perturbations on the surface of the cylinder that cause differences in the boundary layer thickness as flow passes, causing one side to briefly slip faster than the other. The momentum of the vortex continues over to the other side of the cylinder, which increases the fluid pressure on that side and thus slows flow. As pressure always wants to equilibrate, this process reverses and a competing vortex is sent spinning to the opposite side. If flow conditions do not change, this process will continue indefinitely.
In mathematical terms, fluid particles will accelerate over time—∂v / ∂t—towards areas of low pressure—- ∇P (or decelerate if they are already traveling away from an area of low pressure). In order to figure out whether a particular particle will accelerate (or decelerate) towards a certain area of pressure, you'd have to examine the direction magnitude component partial differentials of the velocity and term, ∇2U. In other words, the grad (∇) symbol is a shorthand for the fact that you're looking at something that changes in more than one linear dimension (in the case of this simple 2D model, ∇ denotes that the variable will change in both x and y).
In a 3D model, the same patterns hold true. Let's look at a particle model of the same process. The SPH-generated models below (and all others in this module) show the motion of ~105 particles. Particles in the first plot here are given colors based on the x component of their velocity.
In the second plot, particles are given colors based on their vorticity.
As a fluid becomes less viscous, the momentum term will begin to dominate the Navier-Stokes solution, meaning that the internal shear strength of the fluid is less able to keep it from deforming. As we said before, in this flow past a cylinder model, that means vortex shedding will become more and more viable at either lower viscosities or higher velocities.
Real-world applications 2
Pictured at right, a GPS survey staff causes a slight flow instability downstream.
As beautiful as they are, von Kármán vortex streets are an engineering problem in many real-world applications. Vortex shedding can put enormous shear forces on mechanical joints, which can suffer brittle failure.
The photos above show a weld joint that has failed due to shear forces caused by vortex shedding. At the time of failure, the vessel was traveling about 2-2.5 m/s. Luckily, the mount was secured with rope and the instrument was not lost.
Low pressure behind a cylindrical marine survey mount pole can cause approximately an order of magnitude more drag than a hydrodynamic shape like a teardrop, even at low speeds. Stainless steel "fairings" are sometimes used to reduce this drag and stop the pole from flexing normal (perpendicular) to the direction of travel. Think back to the vorticity and pressure plots from the flow past a cylinder model above. Can you explain why a teardrop-shaped mount would result in more stable flow?
Below are velocity, shear rate, vorticity, Reynolds number, and pressure plots generated in COMSOL for the same fluid flowing around a teardrop-shaped object instead of the cylinder. Compare these to the plots shown above for the cylindrical impediment. You may still notice signs of oscillating flow resulting from the disturbance, but flow is much more laminar. Can you explain why this might be?
Pay attention especially to how the velocity vectors change (or do not change) throughout time. Compare this to the velocity from the water model with the cylindrical impediment. What does this indicate about the differences in inertial forces between the two scenarios?
This looks vastly different from the vorticity plot for the cylinder model.
Note how much lower the cell Reynolds number is compared to the cylinder model!
This also looks vastly different from the pressure plot for the cylinder model. It's amazing how such a simple design can result in a major shift in flow around the object. How does the teardrop shape influence the pressure and vorticity?
Now, let's take a look at this behavior in a fluid with two orders of magnitude less viscosity than water: air.
3) Air (μ = 10-5 Pa s)
Air has a viscosity of μ = 10-5 Pa s (still holding density and velocity constant). How do you think this will affect the deformation of the fluid?
Velocity (x-component) 3
Compare this velocity plot to the velocity from scenario 2 (Water). The initial velocity of the fluid is the same for both scenarios. Why might the maximum velocity be higher for one versus the other?
Note: The scale bar is different between the two.
Shear rate 3
Compare this shear rate plot with the one above. Why is this one "sharper," i.e. the velocity gradient is more severe across the shear zone? What about air in comparison to water allows that to happen?
Vorticity magnitude 3
What is happening to the vorticity as the fluid moves further past the cylinder? Energy from the disturbance propagates forward and eventually dissipates. Can you see where this is happening from each of other variable plots as well?
Pressure 3
In this plot, pressure is not only oscillating back and forth upstream of the cylinder, it seems to be oscillating in the channel behind it as well. Pressure oscillations that occur under these fluid conditions may be occurring near what's called a resonant frequency for this channel.
Reynolds number 3
These cell Reynolds numbers are several orders of magnitude higher than those calculated for the water scenario. In this case, the Reynolds number is above the critical number of 100, which makes it a "transitional" flow. In the range of transitional Reynolds numbers, 100 to 105, eddy-like vortices begin to form and propagate downstream. This phenomenon is much easier to visualize using a 3D particle solution. Let's look at the SPH models for this scenario.
Note: The stippling is an artifact of the meshing process in COMSOL.
Discussion 3 - Air
This specific type of oscillating flow is called a von Kármán vortex street (VKVS), named after Theodore von Kármán, the Hungarian-American physicist who first described it in detail. The process that leads to this type of flow is called vortex shedding. Let's take a deeper look at how these vortices are forming by looking at the particle solution generated in SPH.
These von Kármán vortex streets refer to the double row of vortices being shed from either side of the cylinder. The vortices formed from one side rotate in the opposite direction as the vortices formed from the other side. Each respective vortex row is referred to as a vortex street. Notice that angles at which the vortexes are moving relative to each other.
Compare the vortices here to those generated in the water flow around a cylinder model. What stands out to you about these vortices and what do you think is causing those differences? The ability of these vortices to maintain their form and stability through the entire simulation is remarkable. What do you notice about how they change over time and space? You may notice that these vortices are spaced differently and that they are different sizes than those from the water flow model. These VKVS can be described using several parameters:
The geometry of a VKVS can be defined by two dimensionless ratios, their aspect ratio and their dimensionless width. The aspect ratio is equal to h/a where h is equal to the separation distance between 2 the counter-rotating vortex streets and a is the the distance between 2 vortices in the same vortex street. What would you estimate this ratio to be for the vortices above? The dimensionless width of the VKVS is h/D where D is the diameter of the obstacle (cylinder in this case). In other words, the dimensionless width is just the ratio of the vortex street width to the width of the obstacle. What would you estimate the dimensionless width to be for the vortex street above? These parameters allow us to compare the geometry of vortex streets that vary vastly in size scale. The stable aspect ratio and dimensionless widths observed in lab settings are 0.28 and 1.2, respectively. How do these compare to those you calculated for this VKVS?
The vortex shedding frequency of a VKVS can be calculated from its Strouhal number, which describes the periodicity of oscillating flow mechanisms. The Strouhal number (St) is calculated using the frequency of vortex shedding (f), the obstacle/object diameter (D), and the flow velocity (u): St = f*D/u. Knowing the cylinder diameter (0.1 m) and the flow velocity (1.0 m/s), can you count the vortex shedding frequency from the animation to calculate the Strouhal number of this VKVS?
These von Kármán vortex streets are well-studied fluid phenomena that occur during the transition to turbulence (when 100 < Re < 105). Vortex shedding has many real-world engineering and design applications, some of which were described in the water flow discussion. Next, let's learn about their atmospheric counterparts!
Real-world applications 3
Atmospheric instability
Kármán vortex streets have been thoroughly-modeled in lab settings, but they occur naturally more often than you might think. In fact, the first VKVS described by Theodore von Kármán were observed in the sky. He noticed remarkable swirling patterns in the clouds forming on the lee side of an island. These VKVS occur on a much larger scale than the VKVS that are modeled in lab settings. In the case of these atmospheric vortex streets, there are vertical forces, atmospheric pressure and temperature gradients, and a whole slough of other factors that influence the geometry and stability of the vortices. Many studies have modeled atmospheric VKVS such as the ones shown in the image to the right.
In the case of these atmospheric VKVS, the island acts as the cylinder in our fluid flow models, creating the flow disturbance. As air flows around the island obstacle, vortex shedding begins and these counter-rotating vortices propagate downwind. Do you notice any other differences between these atmospheric VKVS and the simulated VKVS from our air flow around a cylinder model?
Using the scale bar in the image, measure the linear dimension (D) or width of Madeira. Using a wind speed of 10 m/s and the viscosity of air, can you calculate the general Reynolds number for flow around Madeira using the same steps as you previously did in the module?
Now use the same scale bar to measure and characterize the geometry of these atmospheric VKVS. What's the aspect ratio of the VKVS created by Madeira? The dimensionless width? How do these compare to those values observed in lab settings?
Truck tail fairings
Have you ever gotten a little too close to the back of a tractor trailer on the highway and noticed that your car was being buffetted around side-to-side in the wind? If so, you have experienced the effects of von Kármán vortex streets firsthand.
If you've ever seen a tractor trailer with panels hanging off its tail (see image below), you've also seen strategies to counter the effects of vortex shedding firsthand. Remember the marine survey mount fairings from the previous Real-world applications section? These trailer fairings serve essentially the same purpose: reducing drag and causing a more aerodynamic slipstream. The following image is an example of a commercial application of fluid dynamics.
This image shows the effects of creating a more efficient slipstream which reduces vortex shedding and improves fuel efficiency. One estimate claims [2] that these tail fairings can increase fuel efficiency by approximately 10% over hauling distances. Have you thought about why this works? What about the truck and survey pole fairings decreases that instability and allows less vortex shedding?
Conclusions
This module has walked you through various stages in the transition to turbulence. Can you describe this transition in your own words? We have shown you fluid systems with varying levels of predictability. In addition, this module introduced you to some of the tools that you can use to qualitatively and quantitatively characterize fluid flow as well as the physics behind it. The Navier-Stokes momentum equation governs the fluid particle motion while the Reynolds number describes the flow regime. The von Kármán vortex streets generated in transitional flows can also be characterized by their aspect ratio, dimensionless width, and vortex shedding frequency (Strouhal number). Now that you have explored the transition to turbulence through models of fluid flow around a cylinder, you can use your knowledge to examine turbulence and flow behavior in other fluid systems!
Bonus: Complex flows
Although our module focused on models of simple fluid flow, more complex flows make up the vast majority of flow behavior you'll encounter in the real world. It's important to note that the systems modeled above above are highly simplified in order to highlight the physical forces acting on fluids. Below are some examples of more complex flow systems that one might encounter in the real world.
Fully turbulent flows
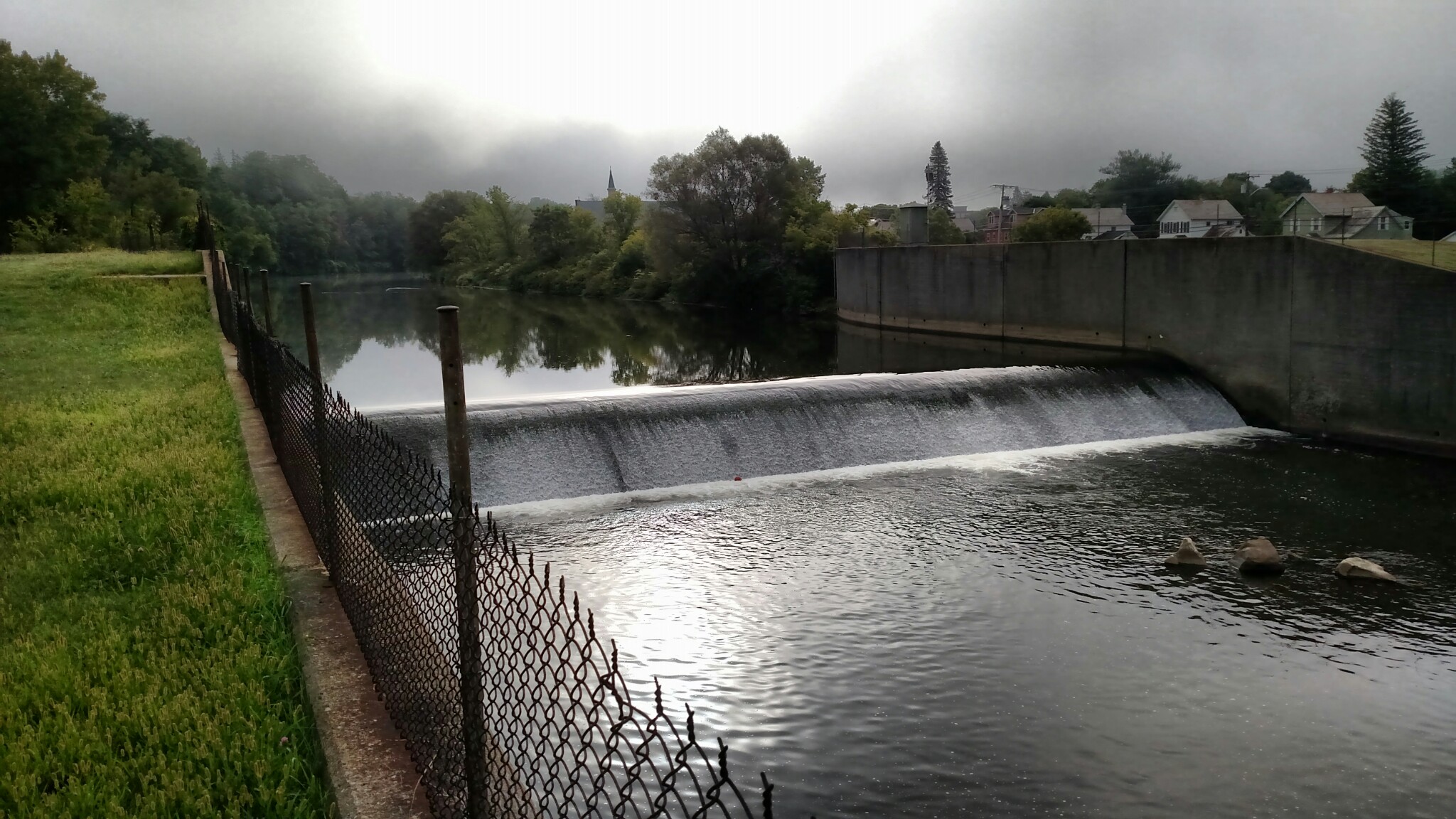
Fully turbulent flow, where 105 < Re and predictability over a scale larger than a couple of particles or beyond a couple of time steps approaches zero, is very difficult to model. In some cases, flows of this nature are easier to compute and the solutions are better represented by Smoothed Particle Hydrodynamic models, in which individual particle smoothing kernels, rather than mesh elements, define the behavior of the fluid. However, flows in high Reynolds cases are are difficult to describe mathematically, and thus solutions that approach full turbulence in continuum or smoothed particle models can take orders of magnitude longer to compute.
The gif above was filmed on August 28, 2011, near peak flow during Hurricane Irene, the current flood of record for USGS gaging station 01332500 near Williamstown, MA. The video shows flow over a US Army Corps of Engineers (USACE) flood control structure (also pictured at baseflow on right). The concrete-bedded flood control flume has low bed roughness and thus high velocity, and comparatively lower Re. Flows like this can be very erosive when they encounter a jump in bed roughness due to a transition from a flood-control flume with a concrete bed to natural (rougher) bed conditions. The purpose of induced turbulence—from USACE's perspective—is to limit scour caused by a sudden increase in bed roughness. By increasing turbulence and thereby reducing friction at the boundary layer, the flow will not be quite as erosive in its transition between bed conditions. The flow captured in this video is at or near the flood control project's design capacity to limit the destructive nature of the flow, and thus this event still eroded cobble- and boulder-sized particles from the natural bed.
"Multiphase" flows
Using a particle physics solution, one can model fluid particle behavior without the need for computationally remeshing, which can have substantial processing power overhead in a continuum model. In this case we use the word "multiphase" to describe the use of two fluids, each with different properties, to initialize the model. The following GIF shows a DualSPHysics two-phase example model of a dam break, where a parcel of water flows over and deforms denser substrate (sediment) material. This type of model can be used to examine physical processes of erosion at a small scale, and potentially could be used to reproduce and expound on results of physical modeling studies of these phenomena.
As you can see here, water flowing on the surface of the sediment creates shear stress at the bed, which both deforms the sediment to certain depths, and entrains grains from the surface. You'll notice that as the front of the flow takes on sediment it behaves more like a debris flow than a water wave. This has the effect of buoying dense sediment up to the surface, which then remains entrained as the flow hits the wall and begins to curl around. From the DualSPHysics documentation:
These multi-phase sediment scouring phenomena are induced by rapid flows creating shear forces at the surface of the sediment which causes the surface to yield and produce a shear layer of sediment suspended particles at the interface and finally sediment suspension in the fluid. Applications include scouring in industrial tanks, port hydrodynamics, wave breaking in coastal applications and scour around structures in civil and environmental engineering flows among others.
Some of the more relevant physical properties of this model are shown in the following table.
Fluid properties of multiphase model | |||||
---|---|---|---|---|---|
Fluid | Density (kg m-3) | Viscosity (Pa s) | Speed of sound (m s-1) | Cohesion coeff. | Angle of internal friction (deg) |
Water | 1000 | 0.001 | 80 | 0 | 0 |
Saturated sediment | 1500 | 0.002 | 81 | 1 | 35 |
A physical multiphase model typically involves a flume, a pump, and a specific particle size or range of sizes to test the effects that flow-induced boundary stress will have on particle saltation, sliding, and entrainment. A simple sediment flume demonstration conducted by Dr. Ronadh Cox (Williams College) is shown below. Apart from the geometry, one major difference between this physical model and the numerical one is that the grain density is that of quartz (2650 kg m-3) in the physical model.